Technology revolutionizes cement production, reducing CO2 emissions by almost 100%
A team of engineers from UCLA developed the ZeroCAL method, capable of eliminating up to 98% of CO2 emissions associated with cement production. Find out more here!
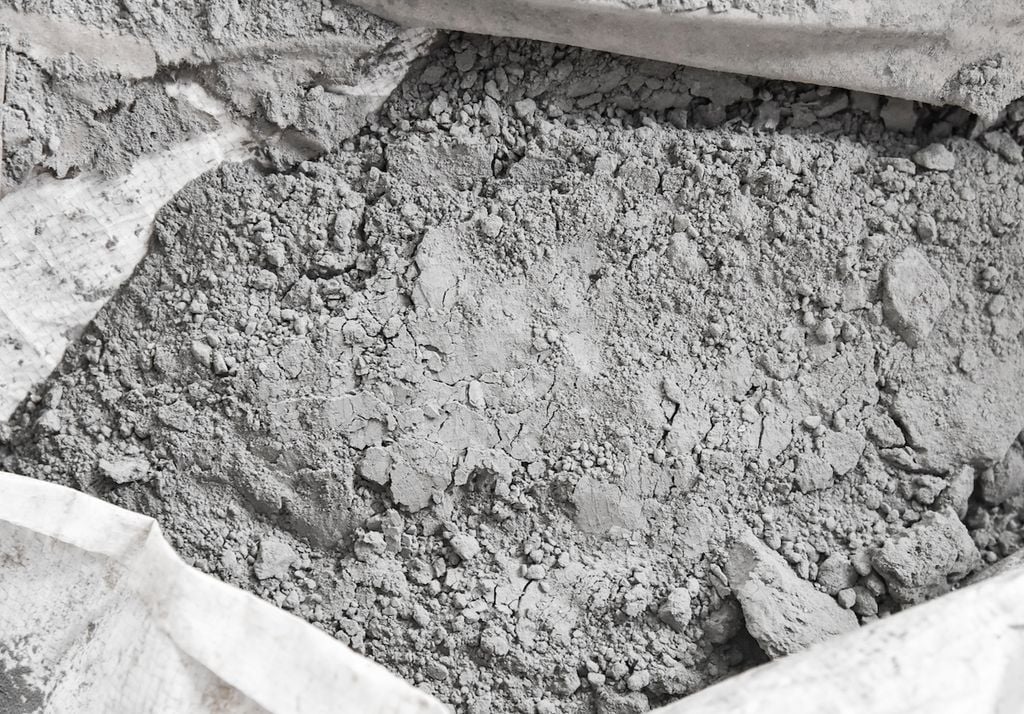
A team of UCLA engineers has developed an innovative process, called ZeroCAL, which can radically transform the cement industry by reducing carbon dioxide (CO2) emissions. Cement, one of the most used materials in the world, is also one of the largest contributors to global greenhouse gas (GHG) emissions.
This method presents itself as an affordable and scalable solution to decarbonize cement production, using existing infrastructures.
The environmental impact of cement
Portland cement, used in concrete production, is the most common type of cement in the world. However, its production has a significant environmental impact. For each kilogram of cement produced, approximately one kilogram of CO2 is emitted. This process is responsible for about 8% of global CO2 emissions, an alarming value that positions cement production as one of the main responsible for the climate crisis.
Much of these emissions are due to the thermomechanical decomposition of limestone, which is the main precursor of lime production, an essential component of cement. 60% of CO2 emissions come from this chemical reaction, and the remaining 40% result from the use of fossil fuels to heat industrial furnaces where the cement production process takes place.
UCLA engineers develop scalable process to decarbonize cement production - ... assistant professor of civil and environmental engineering at UCLA Samueli. We believe the ZeroCAL process offers a unique pathway to enable ... - https://t.co/YuV5WreEql
— The Postdoctoral (@thepostdoctoral) October 14, 2024
In addition to emissions, the process also consumes large amounts of energy. To produce a metric ton of lime, about 1.4 megawatt-hours of energy are needed, the equivalent of the energy consumption of a North American house for a month and a half.
ZeroCAL: An innovative solution
The UCLA team, led by Gaurav Sant, director of the UCLA Carbon Management Institute (ICM), created the ZeroCAL process, which stands for "zero carbon lime", with the aim of eliminating up to 98% of the CO2 emissions associated with lime and cement production. Instead of using traditional limestone, the new method uses calcium hydroxide as a precursor of lime. When heated, this compound emits only water vapor, thus eliminating the production of CO2 during the heating process in the furnaces.
ZeroCAL technology begins with the dissolution of limestone in an aqueous solution containing ethylenediamine tetra-acetic acid, a common industrial acid. Through membrane nano-filtration, calcium is separated from limestone, and then used in an electrochemical process to produce calcium hydroxide.
This process not only eliminates CO2 emissions, but also generates useful by-products, including hydrochloric acid, sodium bicarbonate, oxygen and hydrogen. Hydrogen, in turn, can be used as clean fuel to heat cement furnaces, creating a closed cycle of zero emissions.
In addition, this technology can be implemented in existing cement plants, without the need to build new infrastructures for carbon capture and storage.
Global collaboration and the potential for scalability
Although the ZeroCAL method still requires more energy than traditional processes, the team of researchers is exploring ways to optimize energy use, simplifying operations and reusing the acid and basic co-products resulting from the electrochemical process. To reduce water consumption, researchers suggest the implementation of ZeroCAL in factories located near water sources, such as rivers or coastal areas.
Currently, the UCLA team is working with Ultratech Cement Limited, the largest cement manufacturer in India, to build a demonstration plant that can produce several tons of lime per day using the ZeroCAL process. India is the second largest cement market in the world, and the success of this plant could represent a major breakthrough for the decarbonization of the global cement industry.
The future of industrial decarbonization
The innovation of the UCLA team may have impacts beyond the cement industry. Researchers believe that the ZeroCAL method can also be applied in steel production, another industry with high carbon emissions. In this case, low-carbon lime could be used as a source of calcium in the steelmaking process.
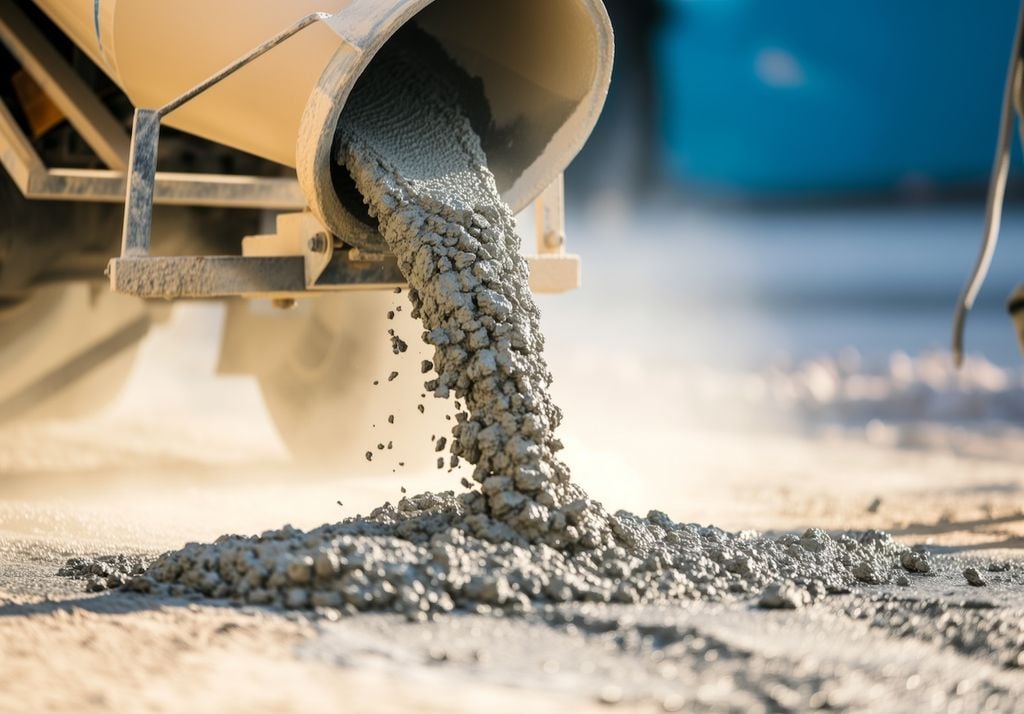
This project was funded by several entities, including the Chan-Zuckerberg Initiative, the Grantham Foundation for the Protection of the Environment, and the U.S. Department of Energy's Advanced Research Projects Agency–Energy.
With this new technology, the UCLA team has taken a significant step towards a more sustainable industrial future, paving the way for emission-free cement production and drastically reduced environmental impact.
News reference:
Leão, A., Collin, M., Ghodkhande, S., Bouissonnié, A., Chen, X., Malin, B., ... & Sant, G. (2024) ZeroCAL: Eliminating Carbon Dioxide Emissions from Limestone's Decomposition to Decarbonize Cement Production. ACS Sustainable Chemistry & Engineering. 10.1021/acssuschemeng.4c03193